The purpose of this report is to feedback on my visit to the Berendsen plant in Copenhagen at the end of April 2017. I was part of a group of 4 together with 2 colleagues from Tibard Laundry and another from Imperial Laundry.
First, I would like to give thanks once again for this opportunity. It was really refreshing to get out of the office and experience how another laundry operate, especially one as progressive as Berendsen. The message from Berendsen throughout was very clear – Efficiency, Efficiency, and Efficiency.
I came away with a lot of ideas which I hope to be able to implement at PLS. Some of which are:
- An email system between the back and day shift Production Supervisors. I have since requested for a copy of this email (attached) and plan to adapt it for our needs. I believe this will not only improve communication between our supervisors but it will also give them more ownership over their work.
- At the first plant, I had the opportunity to speak with the Office Manager and we looked at the Berendsen portal – Connect. Customers enter their order which is processed and tags printed out.She also showed me how abused stock are dealt with. The factory emails through photos which are then forwarded to the customer and they are subsequently charged. This is a process I would like to explore further as educating customers about abused stock is an ongoing battle
- Labelling cages by colour depending on the day of week it has been collected to ensure we process the earliest collected cages first.
- Instigating a formal Reject process. The first plant we visited had dedicated staff responsible for all rejects and these were bagged in yellow bags by customers. Rejects were then examined and where possible, mended, washed at a higher temperature, but if not, discarded.While it is not financially viable at the moment for us to have staff dedicated to examining rejects, Donna, at Imperial Laundry, mentioned that they include a Reject bag with every delivery. I have since suggested we follow suit and disposable purple bags are currently being ordered to be included with each delivery.While our overall reject level is low, there is room for improvement as dedicated bags of reject will instigate a further examination thereby sifting out old linen from the pool. This will give us more accurate stock count as well as being a cost saving from not having to process these linen and losing them in the pool once again.
- The final plant we visited specialised in healthcare and they were most advanced with RFID. We learnt about the process of when the linen returns to the plant, at which stage of the wash process it is at, when it gets delivered, and how long it has been at the customers’. After 150 days, any unreturned items are considered lost and customers are charged the replacement price.We are in the process of chipping our towels and are very much at the beginning of this journey, but as a company, we believe that RFID will not only benefit us financially in the long run but it will also give us greater control over our linen. Therefore, seeing this in action at Berendsen was very exciting and eye opening.
- On a fun note, I noticed several feel good factors at each of the plants like complimentary tea/coffee for all staff, a fussball machine, a dog friendly reception and last but not least, all the General Managers were dressed in denim. It may not seem like a lot but I think small gestures like these makes the workplace.While I was unable to attend the first meeting at the Berendsen headquarter due to the time of my flight, I have thoroughly enjoyed the rest of the trip.It was an invaluable experience and such a pleasure meeting Donna, John, and Aimee. We even managed to squeeze in a visit to The Little Mermaid which made Aimee very happy indeed!The size of the group was just right and we were able to get to know each other over meals and while driving to the plants.
We think it would be splendid to keep up the friendship and if there would be opportunities in the future to meet up in other events or even to visit our respective laundries.
Thank you once again for this opportunity!
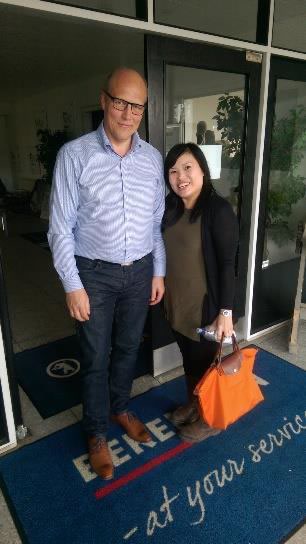